Entrevista Realidad Económica
¿Cómo funciona la única planta de biogás de la región?
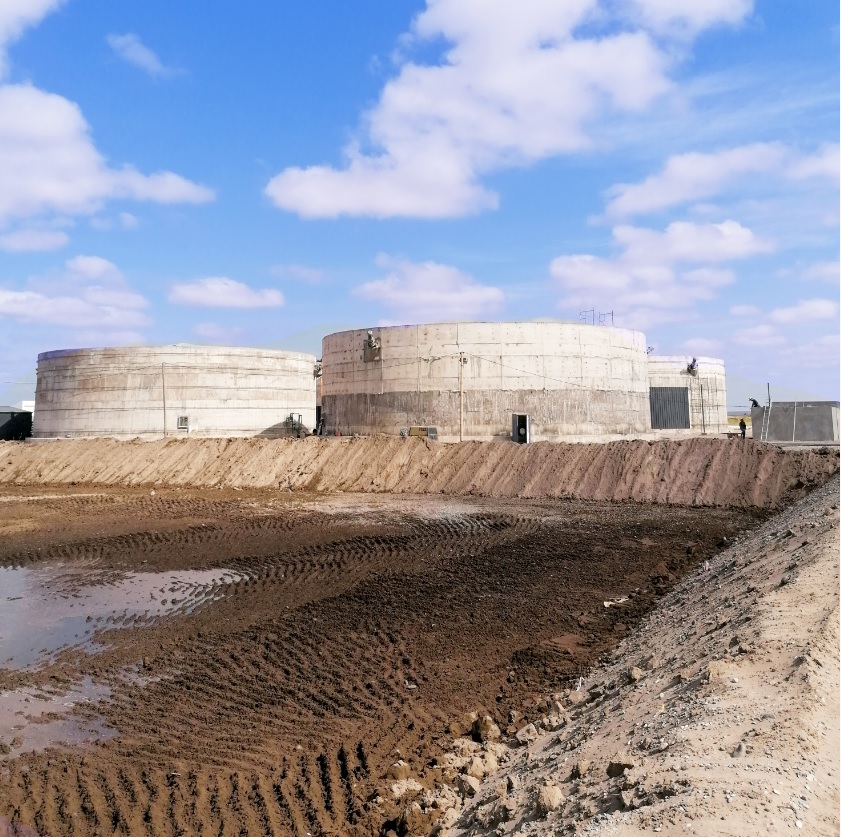
En 25 de Mayo (La Pampa) se está desarrollando un proyecto innovador, único en la zona, que combina producción agroganadera con energía renovable. Se trata de una planta de biogás para producir dos megas de energía e inyectarla a la red nacional a partir de un campo productivo con 3.000 hectáreas.
La empresa AB Agro viene trabajando con sus 1.000 hectáreas de maíz, otras 1.000 hectáreas de alfalfa y pasturas, todo eso para producir forraje, y tienen un engorde de 4.000 animales. El ciclo se completó con la creación de AB Energía, la encargada de gestionar una planta de producción de biogás que requirió una inversión de 9 millones de dólares. “Se trata de 4 tanques de 4.500 metros cúbicos cada uno, se tuvo que importar de Alemania gran parte de las herramientas de la maquinaria porque acá no hay muchas plantas en el país.”,dijo Daniel Barruti, gerente operativo de la planta.
¿Cómo surgió la idea?
Esto inició en 2018 cuando estaba en vigencia el programa Renovar con licitaciones públicas para distintos tipos de energías renovables. Nosotros teníamos el engorde a corral, teníamos (y seguimos teniendo) nuestro propio maíz bajo riego, tenemos el Río Colorado y le queríamos dar un valor agregado a nuestra producción.
Así surgió la idea de producir energía renovable a partir del biogás. La materia prima la teníamos y nos pusimos a trabajar en el informe de impacto ambiental, que nos llevó todo el año 2018.
Cuando fue aprobado ese informe pudimos firmar un acuerdo con Cammesa (Compañía Administradora del Mercado Mayorista Eléctrico Sociedad Anónima), que es el administrador nacional de energía, y entramos como agentes mayoristas del sistema.
Y en marzo de 2019 iniciamos la construcción de la planta. Los digestores se iban a hacer en acero, como lo hace la mayoría en Alemania, y después el dólar marcó otro camino. Tuvimos que agudizar el ingenio para hacerlos de otra cosa y los hicimos de hormigón. Nos llevó casi dos años por la pandemia y en marzo de 2021 empezamos a generar los 2 MW por hora, que era el compromiso que habíamos asumido.
¿De cuánto fue la inversión?
La inversión fue de alrededor de 9 millones de dólares. Se trata de 4 tanques de 4.500 metros cúbicos cada uno, se tuvo que importar de Alemania gran parte de las herramientas de la maquinaria porque acá no hay muchas plantas en el país.
A esta altura creo que hay 27 en todo el país. Tuvimos que importar todo, varias partes de Alemania, los motores de España y de Italia se trajeron materiales para el tratamiento de lo que se está incorporando a la planta.
Y finalmente ya están produciendo…
Estamos en plena producción pero no estamos exentos de la complicación de la importación. Gran parte de los repuestos tienen que venir de afuera. Las cosas se rompen porque esto trabaja 24/7, todo el tiempo y todos los días.
Tenemos todo un sistema de previsibilidad, minimizamos los efectos pero siempre tenemos alguna situación. Además los componentes tienen una vida útil por la propia función que tienen dentro del mecanismo está limitada desde fábrica.
Por ejemplo, una bomba que introduce a la planta todo el material que nosotros incorporamos tiene partes que cada 6, 7 u 8 meses se rompen. Esto lleva tiempo y va cambiando a lo largo del año. A principios de 2022 en 60 días lo teníamos y ahora el plazo se alargó a 180.
En el engorde a corral los efluentes sólidos son un problema importante. ¿Lo resolvieron con la planta?
Si, totalmente. Con esto resolví el problema de los efluentes y pasó a ser un material valioso para nosotros. Con 4.000 animales encerrados estamos produciendo diariamente entre 40 y 60 toneladas de efluente. Es muy importante.
La energía que utilizamos en el campo, por ejemplo, para los equipos de riego, la compramos a la cooperativa local. Lo que generamos va directamente a la red, el proyecto está armado así.
Lo que tiene planta te genera energía eléctrica, térmica y después también está en cada uno como la utiliza. Nosotros la usamos para calefaccionar los tanques y está previsto que también se use para otros sustratos de origen frigorífico que necesitan temperatura para pasteurizar y homogeneizar.
Se lo podría usar para calefaccionar una casa, un invernadero, para una planta de secado de alfalfa, para un montón de cosas. Además, esa agua circulante que es para refrigerar los motores se puede reutilizar. Lo mismo que el gas del escape.
Gran parte de esa energía no la estamos usando porque hace poco la estamos generando.
Y estaban llevando desechos del lúpulo del Valle, ¿no?
Si, tenemos una economía circular interprovincial. Nosotros incorporamos a los digestores el descarte del maíz, el efluente sólido del ganado, el bagazo de cerveza… Todo eso pasa por un proceso de 60 días en el que se le quita el biogás, se saca el metano y toda esa materia orgánica degradada sale por la otra punta, va a un separador que saca la parte líquida de la solida. Esta última, que es un biofertilizante, la incorporamos al campo y la parte líquida la sumamos a los equipos de riego también para fertilizar. Es una economía circular.
AB Energía y AB Agro van en paralelo…
AB Energía fue creada porque teníamos la obligación de constituir una empresa para comercializar la energía. AB Agro es el campo, es la estructura que lo rodea.